Characteristics of MQL
In the metal cutting process, cutting fluid is usually used. Cutting fluid mainly plays the role of cooling, lubrication, chip removal, and rust prevention, which helps to improve the tool durability and reduce the thermal deformation of the workpiece, ensure the surface quality of the workpiece.
But a lot of cutting fluid has also caused a lot of adverse effects, not only resulting in increased production costs, but also to the environment and human health has brought enormous potential harm.
According to the data, the cost of cutting fluid is equivalent to 7%-17% of the total manufacturing cost, while the cost of tools is only 2%-4%.
In the face of the requirements of reducing production costs, improving production conditions and implementing sustainable development for environmental protection, rational utilization of manufacturing resources, less waste, less environmental pollution and high safety, “Green Cutting” technology, which can be used in a virtuous circle, is one of the leading development trends in the field of advanced manufacturing.
Minimum Quantity Lubrication (MQL) is a kind of green processing technology with excellent development potential and broad application prospects.
- Micro-lubrication, also known as semi-dry cutting or quasi-dry cutting, is the vaporization of compressed gases (air, nitrogen, carbon dioxide, etc.) and a minimal amount of lubricating oil to form micron-sized droplets, a cutting method that sprayed into a machining area for adequate lubrication.
- The primary role of micro-lubrication is lubrication, which plays a role in reducing friction, cutting hot rivers to improve the flow of chips.
- Mql cutting technology dramatically reduces the cost of coolant, makes the tools, workpiece, and chips outside the cutting area dry, improves the working environment, avoids the problem of waste liquid treatment, has distinct application advantages, and wide application range.
An MQL brand structure diagram
- Liquid Storage Tank
- Connector
- Braided Air Hose
- Lubricating Hose
- Air Flow Valve
- Shell
- Oil, Regulation
- Air Filter.
- Precision oil pump
- Control Valve Inlet
- Filter Drain Outlet
- Electromagnetic pulse regulation
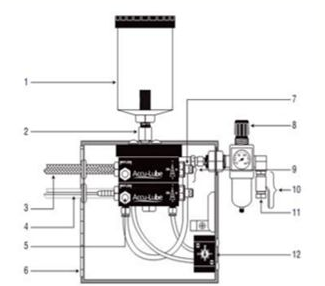
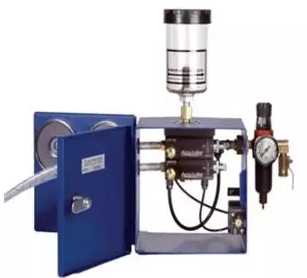
Mql lubrication mode
01 Mist External Lubrication
Mist External Lubrication: the cutting fluid is fed to a high-pressure spray system and atomized in a mixture of gases. The droplets are then sprayed to the surface of the cutting tool by one or more nozzles of up to MM, micron size, cool and lubricate the cutting tool
About the external lubrication system
- The external lubrication system consists of Air compressor, oil pump, control valve, nozzle, and piping.
- The integrated system is a low cost, lightweight, and can be easily installed on machine tools.
- However, because the position of the nose has a significant influence on the lubrication effect, it is necessary to determine the best location and spray angle of the nose, and it is difficult for the externally lubricated mist particles to enter the deep hole drilling processing area, so the cooling and the lubricating effect is not suitable for deep hole processing Externally lubricated fog particles small, easy to fly around, on the working environment will have a positive impact, so the need for supporting protective facilities.
02 Mist inner cooling mode
Mist inner cooling mode: The cooling mist is sent directly to the cutting area through the holes of the spindle and the cutting tool for cooling and lubrication. According to the processing requirement, the two lubrication methods can be used to obtain the best cooling lubrication effect.
About the internal lubrication system
- The internal lubrication system supplies the lubricant through the main shaft and the inner channel of the cutter, which can reach the processing area directly.
- The lubrication is sufficient, and the general effect is better than the external lubrication.
- But the internal lubrication system also has some disadvantages: It makes the structure of the spindle and tool system of the machine tool complex, even affects the working performance of the whole machine tool;
- when the spindle speed is too high, it is affected by centrifugal force, the cutting fluid is easy to stick to the inner hole wall of the spindle and the tool, so it is difficult to reach the cutting zone.
- At present, the spindle speed of the machine tool using the internal MQL technology does not exceed 20000-30000 R / min.
- In order to avoid inertia and gravity influence, the inner lubrication system should consider the fog particle generator.
- The diameter of the fog particle must be small enough to keep the fog particle suspended.
Requirements of MQL for cutting tools
In the micro-lubrication cutting process, the heat absorbed by the lubricant is less, most of the heat is carried away by the chip and absorbed by the tool, so the tool’s performance is required higher.
01
Cutting tools should have excellent high-temperature performance, so the need for a new cutting tool material or thermal protection hard surface coating.
02
The friction coefficient between the chip and the tool should be small, and it is better to have a layer of lubrication film on the top of the hard coating of the machine, to reduce the accumulation of cutting edge.
03
Because the cutting edge of the cutting tool bears high mechanical stress and thermal stress, the hardness and impact toughness of the cutting edge are required to be high, the selection of the geometric parameters of the cutting tool and the cutting parameters should be reasonable.
The cutting tool can be used for rapid chip removal, reduce Heat build-up.
Note:
For the tools in the internal spraying MQL system,
- firstly, the internal channels of the devices should be designed according to the MQL system, and the structural parameters of the tools should be redesigned.
- Secondly, the tools should be designed according to the oil mist inlet and outlet, the entrance should be favorable for the passage of mist particles, and the exit should be well protected against chips.
- Otherwise, the spattered chips will damage the lubricant exit easily.
The cutting performance of MQL
- The results show that MQL exhibits excellent cutting performance compared with dry cutting and wet cutting for titanium alloy, hardened steel, high-temperature alloy, and stainless steel, correct and reasonable use of MQL can effectively improve tool durability, improve the surface quality of workpiece processing.
- Due to the high cutting temperature of conventional MQL technology, the lubrication effect of cutting tool surface will be increased when the cutting temperature is too high if the temperature of the existing Compressed air can be significantly reduced, then, on the one hand, the intensity of heat transfer in the cutting zone can be increased, and the heat transfer effect can be improved; on the other hand, the improvement of the heat transfer effect can make the lubrication film formed on the surface of the tool to keep the lubrication ability further, so as to improve the tool durability. If MQL combined with nitrogen, MQL can perform better-cutting performance; this is mainly due to the role of nitrogen-oxygen.
- Yes, and the field of application is limited. Micro-lubrication technology is an effective green manufacturing technology, which has prominent advantages in lubrication, chip removal, and so on. As a new lubrication technology, low-temperature MQL technology is convenient to be used in the machining field, high-speed machining of difficult-to-process materials such as superalloy and high hardness has excellent properties, which can further improve the machining efficiency and quality of difficult-to-process materials on the machine tools.
Q: Single / Double Channel Selection problem
- In an MQL system, there are two basic ways of mixing air and lubricant. The single-channel internal cooling tool MQL system combines the two components in a reservoir behind the spindle and then passes through a pipe through a rotating union joint, the mixture of air and lubricant is conveyed to the head of the knife through the rod and the knife tower.
- The dual-channel internal cooling tool MQL system is a circulatory system in which lubricant is continuously pumped from a reservoir and stored in a circular tube. To provide a precise amount of oil, a quick-acting valve in front of the Rotary Conveyor used to regulate the amount of lubricant entering the system. When the MQL system is required to operate, the quick-acting valve is opened to extract the optimum amount of oil from the ring pipe.
- A precise amount of lubricant is delivered to the nozzle at the back of the handle through a spray rod at the center of the spindle. When the lubricating liquid enters the nose through the spray Rod, the air supplied by the rotating conveying device enters the mixing chamber of the nozzle along the cooling passage around the central axis of the shower rod, and the sky and the lubricating liquid are mixed in the mixing room to Form Gas Mist. The mist then flows through a cooling hole in the tool and is ejected as an excellent lubricant / Air Particle.
- Spindle speed is a factor to consider when selecting A SINGLE-OR DUAL-CHANNEL MQL system. The single-channel system mixes the lubricant with air before passing through the spindle, so the maximum allowable spindle speed is about 16,000 R / min. This is because centrifugal forces at higher rates may cause the lubricant to separate from the air. The dual-channel system is suitable for spindle speeds up to about 40,000 R / Min.
- Also, for a single-channel system, the flow distance of the spray is limited, and the maximum flow is about 1270 mm before the flow rate slows down. This is not a problem for a standard machining center. Still, for a large Gantry machining center, a single-channel system is installed on the Longmen body so that it can move with the Gantry, the MQL system can not place on the ground, and long-distance transport fog.
Leave A Comment