Definition of boring
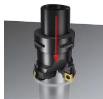
Boring: The process of cutting the surface of a workpiece by the relative movement of the boring cutter and the workpiece, so that a layer of metal removed from the machined surface and the machined surface machined to a certain degree of accuracy and surface roughness.

Difference: compared with other hole processing technology, boring is not limited by the size of the cutter, and boring has a strong error correction ability, can correct the error of the original rough hole axis through repeated cutting, and the position accuracy of the boring hole and the positioning datum can be kept high.
Type of boring cutter
Type 1.
Classification of several edges: single-edged Boring Cutter / double-edged Boring Cutter / multi-edged boring cutter.
Processing Classification: Through Hole Boring Cutter / Blind Hole Boring Cutter / Step Hole Boring Cutter/cross-section Boring Cutter.
Structural classification: Monolithic / Modular / modular.
Type 2.
Single-edged Boring Cutter: Integral Boring Cutter / Welded Boring Cutter / Machine Clamping Boring Cutter / indexable boring cutter.
Double-edged Boring Cutter: Fixed double-edged Boring Cutter / Floating double-edged Boring Cutter
The boring tool module expanded, and the boring tool used to cut the groove
Step Boring Cutter single-edged Boring Cutter Integral Boring Cutter
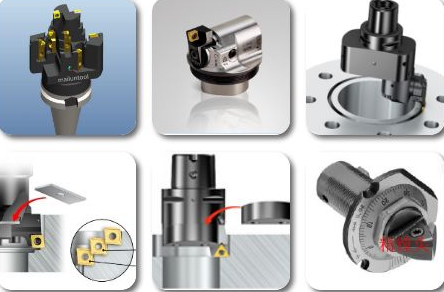
Application of boring-Application of rough boring

It is vital to ensure correct chip removal when machining blind holes.
- The correct cutting parameters are necessary to obtain the proper chip shape.
- Make sure / check that the chips do not clog or wear out the blade.
- coolant hydraulic pressure and cutting fluid flow should be sufficient to allow the chips to drain
- Vertical machines require more efficient chip removal than horizontal machines.

When intermittent cutting such as cross-hole, the cutting condition of the blade is required.
- Choose more ductile materials.
- Under the stable working condition, to improve machining safety, choose a solid square negative rake original shape blade.
- Reduce cutting parameters if there are multiple breaks

The inclusion of sand in the casting increases the wear of the blade.
- Choose more ductile materials.
- reduce cutting parameters.
- To improve machining safety and minimize wear, choose solid square negative rake blades of the basic shape.
PS: Sand inclusion means there is sand inclusion on the casting.

Local areas of air-fired holes may harden, thereby increasing the wear of the blade.
- Choose more ductile materials.
- reduce cutting parameters.
- To improve machining safety and minimize wear, choose solid square negative rake blades of the basic shape.
Application of boring-Application of fine boring

The effect of reducing power on the product
- when the tool is in the cutting state, the tangential and radial components of the cutting force will attempt to deflect the device from the workpiece. The tangential component will try to force the tool down and away from the centerline. In this way, the tool clearance angle reduced.
- Any radial deformation reduces the depth of cut and chip thickness, resulting in a tendency to vibration.

Influence of balancing force on machining
- An imbalance caused by an asymmetric tool or a large stroke, creating an effect on the boring cutter.
- In most applications, the power generated by the imbalance is negligible compared to the cutting force.
- At high speed may cause vibration, which may affect the quality of hole machining
Cases to analyze
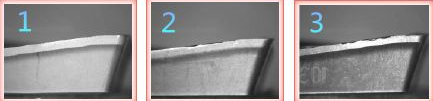
- In the boring process, the tool is continuously cut, which is easy to be worn and damaged, which reduces the dimensional accuracy of the hole processing and increases the value of the Surface roughness.
- leading to adjustment error and deviation of processing aperture and even product quality accident.
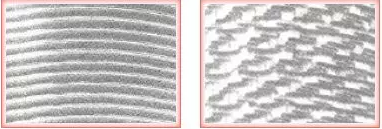
It is a common phenomenon of surface quality to boring fish-scale or thread-like cutting lines of the machined surface.
Left: mainly due to the boring feed and drilling speed mismatch.
Right: mainly due to the boring process of rigid vibration and tool wear
How to use spindle positioning in boring tool machining?
- Using the dial indicator measuring device to find the correct position, we must first use the dial indicator centralizer or positioning Mandrel to determine the coordinates of the reference hole on the workpiece, and then according to the coordinates of the reference Hole, determine the position of the principal axis. The utility model has the advantages of high precision and convenient operation.
- This method characterized by low positioning accuracy and time-consuming. But this positioning method can directly find the coordinate position between the boring machine spindle and the starting hole.
- This method is characterized by the positive orientation of the hole’s interface, which can be used to bring the whole system of the separated box body. The disadvantage is that the auxiliary time is longer.
- This method characterized by a simple template structure and no need for complex adjustment. But the template is easy to deform, and when the workpiece needs to process several holes on different surfaces, it requires several models, alignment, and positioning accuracy is also low.
7 Tips when we meet with problems
Equipment Used
- Spindle speed can be processed
- Coolant supply and pressure
- Whether the machine capacity is satisfied
- Spindle interface selection is correct
- Whether the workpiece clamping stability
- Power selection is reasonable
- Whether the choice of Torque is reasonable
being processed products
- whether the material is good chip-breaking performance
- whether there is a thin-walled part causing vibration
- hardness
machining aperture
- boring diameter
- boring depth
- surface quality
- straightness
- position
- boring tolerance
Leave A Comment